Part 6 - A Worked Example
In the last two posts of this series, I’m going to take the thoughts in the previous posts and apply them to business cases for a couple of real-world examples.
Our first organization is a technology component manufacturer that is headquartered in the US but has operations in four different locations around the globe. They have an impressive patent portfolio but are largely unknown outside of their industry where they dominate. There are architects based in the US, Europe and India but there is no formal review mechanism in place – overlaps and touch-points are resolved on an ad-hoc basis.
Risk Reduction
Regulatory Compliance
The company has two main issues with regards to regulatory compliance. They have to show compliance with various directives on safe disposal of materials, but this is not significantly affected by architecture. However, as a supplier to the US military involved in classified projects that also maintains a multinational presence, they are very much subject to ITAR. Raytheon agreed to pay $8 Million as a settlement for ITAR non-compliance; let’s estimate a 1% reduction in the chance of non compliance due to architectural analysis. That’s $80,000.
Security Architecture
The company’s designs are its value; a security breach would be catastrophic. They turn over $2.5Billion a year. A breach could cost them $100M in revenue – if having a formal architecture model reduces the chance of this by .25%, we have a value of $250k.
Disaster Recovery
They end up restoring from backup 3 times a year, and each time on average 250 employees lose 4 hours of work, at an hourly cost of $120. So reducing this by 10% means a $36k saving.
Operating Cost Reduction
Application consolidation
Application consolidation is seen as a secondary concern in this organization – there’s an assumption that one application will be retired, to a value of $10k.
Reduced System Downtime
Only about 5000 employees are estimated to lose significant time due to outages, however, these tend to be well paid ones, and they lose half an hour each. This makes for a loss of $15k.
Eliminating inefficiencies
The company employs mostly high-functioning designers and manufacturing staff. The network is not a problem. No anticipated value.
Faster analysis and design
There are 20 architects, who will save about 1 hour per project on each of the 10 projects that they get involved in. Value of $20,000.
Revenue Increase
The nature of the company’s business is that it makes high-tech components; interaction between IT and the business is not a core driver, so no value is anticipated here.
Improved Decision Making
Project Estimation
This has historically not been a large problem for the organization – they do not anticipate saving more than 10k annually in this area by having a better picture of their architecture.
Reference Architectures.
Here we will assume that the 200 projects per year each save 1 hour by using reference architectures – for a saving of $20k.
Capability Planning.
The company anticipates that 5 staff will each save 10 hours per year, for an annual value of $5k.
Cultural Changes
The only benefit here is anticipated to be lower staff turnover. Taking the figures from the example in part 3, we get a 15k value.
Data Gathering
Data Import
The company will be importing from 2 tools, each of which will cost 4 days of work at $600 per day. Cost is $4,800.
Import and conversion of existing diagrams
There are about 100 relevant diagrams that the organization wants to import, and they will each take 2 hours. At $100 per hour imputed cost, this gives a figure of $20k
Data Discovery
No extra modeling will be performed, so there is no cost in this area.
Data Rationalization
Data cleaning
The company does want to import a lot of information, but this information is pretty inaccurate, and they have estimated that this will take a data analyst 3 weeks to address at $800 per day – at a total cost of $12k.
Naming conventions
A working team of 10 people will meet 10 times for an hour each time to agree naming conventions, for a total cost of $10k.
Resolving overlaps
This has been identified as an issue in the data imports, and the estimation is that it will take 2 SMEs a week to come up with a process and set of rules for resolving them, for a total cost of $8k.
Communication and rollout
Obtaining buy in
A team of 2 people spend 8 hours creating materials for a roadshow, plus an hour meeting with each of the 10 stakeholder groups, with a further hour for follow up each time. Each stakeholder group sends 2 delegates, so that the total cost becomes $3600.
Establishing Processes
A core working team is going to agree processes; this team will consist of 10 stakeholders, meeting 10 times for an hour each time, with 2 of them as the leads, who perform 2 hours follow up after each meeting to address action items. This comes to a total cost of $13.2k
Training
There are 20 architects, who will each spend a day in tool training; plus, 10 of them will spend a day in specialized modeling training, for a total cost of $24k.
Tooling
Tools
The company has spent 106k on a tool, and will be paying 67k annually.
Tool consultancy
The company has purchased $63k of consultancy.
Governance overhead
Architecture review
The company is imposing a rigorous architecture process, with each of 200 projects requiring an EARC review with 5 people, plus another hour of prep time for the architect involved. At $100 per hour, this works out to $120k annually.
Updating the model
After review, it’s anticipated that each project will require the relevant architect to spend 2 hours updating the production model – for a cost of $40k annually.
So, based on the previous analysis, we get the following;
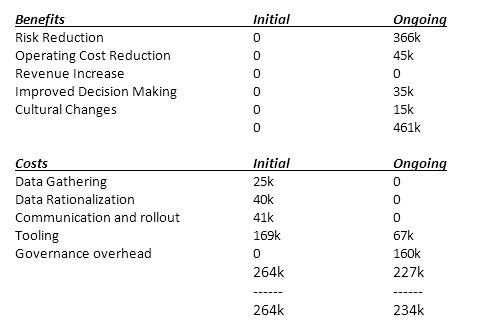
So with the estimations above, the architecture model will lose 30k in the first year, but realize a value of 234k annually thereafter.